Used sparingly, petroleum-based styrene provides resilient cell structures. EPS owes its superior insulating and cushioning properties primarily to the air trapped in the cells.
Step 1: the granules
The chemical process of ′suspension polymerisation′ starts when the liquid precursor styrene is mixed with water and stirred. Droplets and, ultimately, compact granules are formed: plastic beads with a size of between 0.3 and 2.5 millimetres. Pentane that has been mixed in as a blowing agent makes the resulting polystyrene granules expandable into a foam. When exposed to pure steam, they expand up to 50 times their volume and form a highly efficient foam granulate material, complete with innumerable little pockets of air. Alternatively, used EPS can be recycled back into virgin granules by means of extrusion (melting).

Step 2: the added value
Depending on the requirements, the granules can be given special properties, such as ‘pore-deep’ colours or the maximum reflection of heat radiation. This is done by coating the beads or by means of extrusion: To this end, the granules are melted down, mixed with special additives and then dispensed again in grain form. By controlling polymerisation, coating and extrusion, we give sunpor-EPS exactly the properties needed for the respective final application.
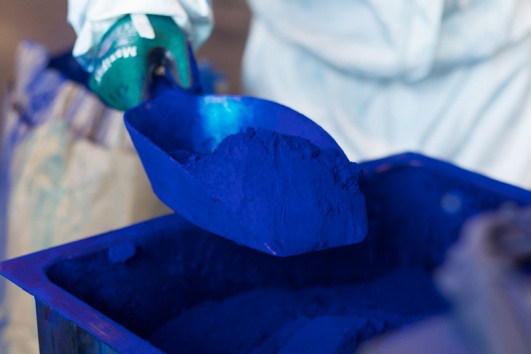
Step 3: the application
Processors, sunpor’s customers, foam up the granulate material and weld it. To do this, they heat it up with steam. The beads expand to 10 to 50 times their volume when exposed to the pentane contained in it as a blowing agent. Now the EPS can be further processed into blocks, boards or moulded parts.
